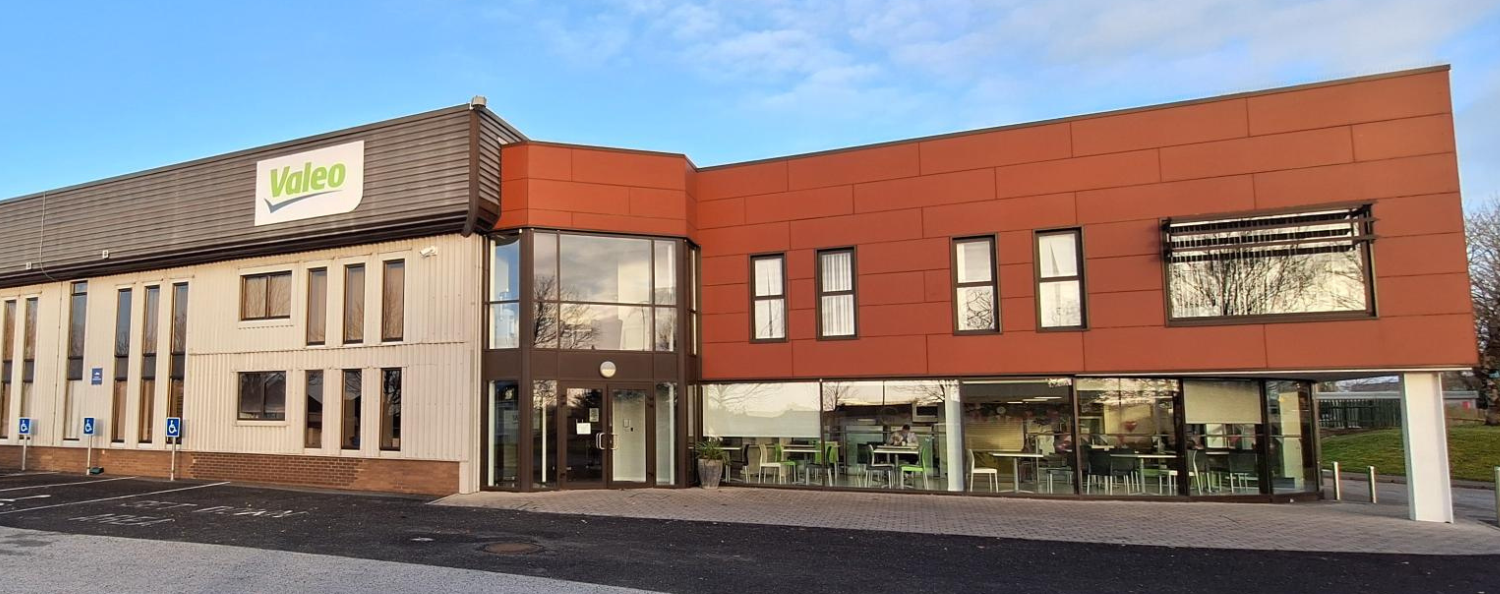
Efficient use of production shutdowns at VALEO VISION SYSTEMS
Standstill costs - time, money and efficiency. Every hour that a machine is stopped means economic losses and potential delays. For our customer VALEO VISION SYSTEMS, we have found a solution to avoid exactly that.
The planned plant shutdown times were used optimally to carry out a comprehensive on-site calibration - without additional production downtime. With our mobile calibration service directly on site, the company was not only able to maintain its usual high quality standards, but also achieve significant time and cost savings.
VALEO VISION SYSTEMS: Technology leader in driver assistance
VALEO VISION SYSTEMS is part of the Valeo Group, one of the world's leading companies for camera systems and driver assistance technologies. The company employs around 850 people at its site in Tuam, Galway (Ireland).
A central component of quality assurance is the extensive test equipment pool with over 1,000 measuring devices. This high-precision measurement technology - consisting of electrical, thermodynamic and mechanical test equipment - ensures that the strict requirements for driver assistance systems are always met.
For the regular calibration of this test equipment, VALEO VISION SYSTEMS needs a flexible and reliable partner who meets international requirements, guarantees maximum efficiency and carries out the complete calibration within the company's closing times.
The solution: Customized on-site calibration
Thanks to our close cooperation with the customer and our Europe-wide flexibility, we were able to develop an efficient and tailor-made solution:
- Accredited electrical, thermodynamic and mechanical calibration - to ensure the highest measurement accuracy
- Flexible on-site calibration precisely during the short-term planned closing times
- Compliance with the highest quality standards thanks to large reference measuring devices Park and internationally available calibration technicians
- Transparent project communication to keep the customer informed of progress, challenges and solutions at all times
The result: higher quality, no additional costs due to downtime and satisfied customers
Through strategic planning and efficient implementation, we were able to ensure that:
- Over 95% of calibrations are carried out on site within the planned time frame
- The remaining measuring devices were also calibrated on time by sending them to one of our calibration laboratories across Europe
- All test equipment continues to meet the highest precision and conformity to standards
- Process reliability and quality have been significantly improved
- Customer satisfaction and long-term cooperation have been strengthened
Without regular calibration and maintenance, you will not be able to meet the normative requirements and your own quality standards. With our precise service tailored to your company, you can counteract this risk in a targeted manner.
With Testo Industrial Services, the company has a full-service provider at its side that provides support with a Europe-wide network of technicians and mobile reference measuring instruments exactly where it is needed - directly on site and precisely coordinated with the planned plant closure times.
Your contact person
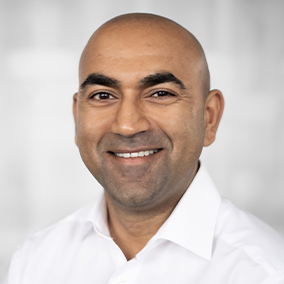